New York City Rising
New York City has always been known for its soaring skyscrapers. In fact, New York was home to the world’s tallest building for an accumulated 86 years before cities in Asia started breaking height records in the late 1990s.
But even today, New York continues to push the limits of tall construction, and Pavarini McGovern is right on the front lines. The firm is building several of the city’s newest towers, including residential towers at 100 Vandam and 200 Amsterdam and the new Pendry Hotel in Hudson Yards.
Building these kinds of structures in a city as active and dense as New York brings a number of expected challenges, from site constraints to infrastructure coordination. But each project (and owner) is different, meaning the project team cannot use a “one size fits all” approach.
Different Project, Different Challenges
All three of these towers are concrete and curtainwall structures reaching to heights of 20 (the Pendry), 25 (100 Vandam) and 55 stories (200 Amsterdam), respectively. They are also all located in Manhattan—so space to do anything on site is limited.
“There is zero room for logistics or lay-down areas,’’ says Marc DePaul, vice president of operations at Pavarini McGovern. “It’s a major challenge to try to fit a tower crane and exterior hoist on a 75-foot-wide property frontage while still leaving room for materials, equipment and laydown.”
While those elements are similar, the specifics of each project’s site and circumstances pose very different challenges for the construction teams. 200 Amsterdam, for instance, is in the middle of a residential neighborhood on the Upper West Side. That means construction noise and working with the community are key focus areas for the project team. To build the tower, however, PMG and its team have had to excavate through roughly 50ft of solid bedrock—which, not surprisingly, can get loud. The team has installed sound-absorbing blankets along the perimeter site fence, as well as wrapped those blankets around the hoe rams and chipping hammers to help reduce the noise of rock chipping and drilling.
“We took a very proactive approach with the community,” says DePaul. “We have an email community outreach program that we use to constantly share the schedule and events and update neighbors on what’s happening with construction sequencing.”
For the Pendry Hotel, noise is not the issue. The acres of development within the Manhattan West and adjacent Hudson Yards sites include multiple construction projects all happening simultaneously. And therein lies the challenge. Brookfield is developing the Pendry, whose full-city-block-sized site includes two high-rise office towers, a high-rise residential tower and the hotel. Needless to say, competition for work areas can get complicated.
“We’re in constant communication with the other construction management firms on a daily basis,” DePaul says. “We all meet weekly to go through site logistics, tower crane locations and swing operations, safety and other site issues, and to coordinate scopes like overtime and weekend work. We have around 30 team members from all of our firms at these meetings, making sure everyone’s project schedule stays on track.”
At 100 Vandam, neighborhood noise and site limitations also apply, but the most pressing challenge comes with the building itself. The project is preserving the building’s original six-story façade, building an entirely new core to support the new stories above. Bracing towers on capped concrete piles keep the exterior walls in place, tying into the building via a steel truss system at the window openings. “The system is designed to avoid impacts to the façade itself and the ongoing work within the walls,” says Sade Obayemi, project executive for Pavarini McGovern. “We’ve also used vibration monitors and other tools to keep a vigilant eye on the façade to make sure there was no impact to the façade as construction continued.”
Preparation is Key
So how does a construction team prepare for the routine and unique challenges that these incredibly complex projects bring? Preparation, says DePaul.
First, he says, the team does a great deal of research when they have even the earliest interest in a project. “We do detailed studies into the site and its logistical constraints and difficulties, plus any challenges we foresee with utility connections or MTA limitations,” he says. “We also work hard to fully understand what the client’s most important needs might be. All of that helps us shape how we will tailor our approach for that project.”
Another key factor, he says, is staffing. “We hand-select the right PMG team members for the job. We match their experience and expertise to the specific complexities of the project at hand.”
All that upfront work has helped Pavarini McGovern become one of the city’s leading companies when it comes to building the towers that define the Manhattan skyline. And, says DePaul, the challenges that come with that are well worth the reward.
“I am most proud of our team when we are awarded one of these amazing projects. It’s a true reflection of all the hard work and dedication that PMG puts in, and the trust the client has in us to do the job.”
Project
crown image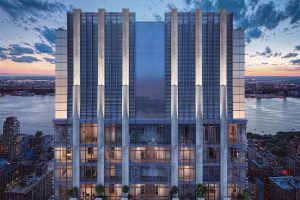
200 Amsterdam
Height: 55 stories
Client: SJP Properties
Architect: Elkus Manfredi/CetraRuddy
Type: Residential
100 Vandam
Height: 25 stories
Client: Jeff Greene
Architect: COOKFOX Architects
Type: Residential
Pendry Hotel
Height: 20 stories
Client: Brookfield
Architect: Skidmore, Owings & Merrill
Type: Hotel
To Crane or Not to Crane?
When it comes to building multistory towers, that is the question. For Pavarini McGovern, whose work is primarily core & shell construction in dense Manhattan, hoisting options are among the first examined as they plan their project approach.
So, what sort of thought goes into deciding if a crane is the way to go? And which crane to use? Turns out, a lot. Here, Ed Lydon, Pavarini McGovern’s general superintendent (and logistical mastermind) shares five primary factors when considering hoisting options.
Building Height.
Typically, once a new building exceeds 30 floors, a tower crane becomes the only option. For 200 Amsterdam, PMG selected the FAVCO 440—a “workhorse” due to its speed and capacity.
Logistics.
In densely packed cities like New York, space on the ground is at a premium. For the Pendry Hotel, the restricted laydown area, heavy traffic and nearby entrance to the Lincoln Tunnel ruled out using a mobile crawler crane. Despite the building’s modest height, PMG optimized precious logistics space by choosing a tower crane to erect the structure.
Budget and Schedule.
While tower cranes are fast and efficient, they are also expensive and can add millions to a construction budget. In some cases, owners and developers may be willing to relax the schedule to save on costs. For those projects, a combination of crawler cranes and “set back” spider cranes can achieve the same high-quality result with a later completion date.
Safety
During crane selection, PMG is very focused on safety—of both the public and construction personnel. Safety considerations include the age and condition of the equipment, past performance, weather implications, proximity to public utilities, transit lines and tunnels and the quality and safety record of the operator and erector. At its own expense, PMG hires a third-party crane inspection engineer to ensure the safety of all crane equipment before it is allowed on any project site.
Owner Priorities
When there are many good options, the final decision can come down to the client. Does the owner appreciate the speed and efficiency of diesel crane construction? Or the quieter and cleaner electric crane? Are they looking to save money by using a street crane, understanding it may mean relaxing the schedule to accommodate delays? It’s important to have an open dialogue with clients early on so they understand the options and the construction team understands their priorities.