United States
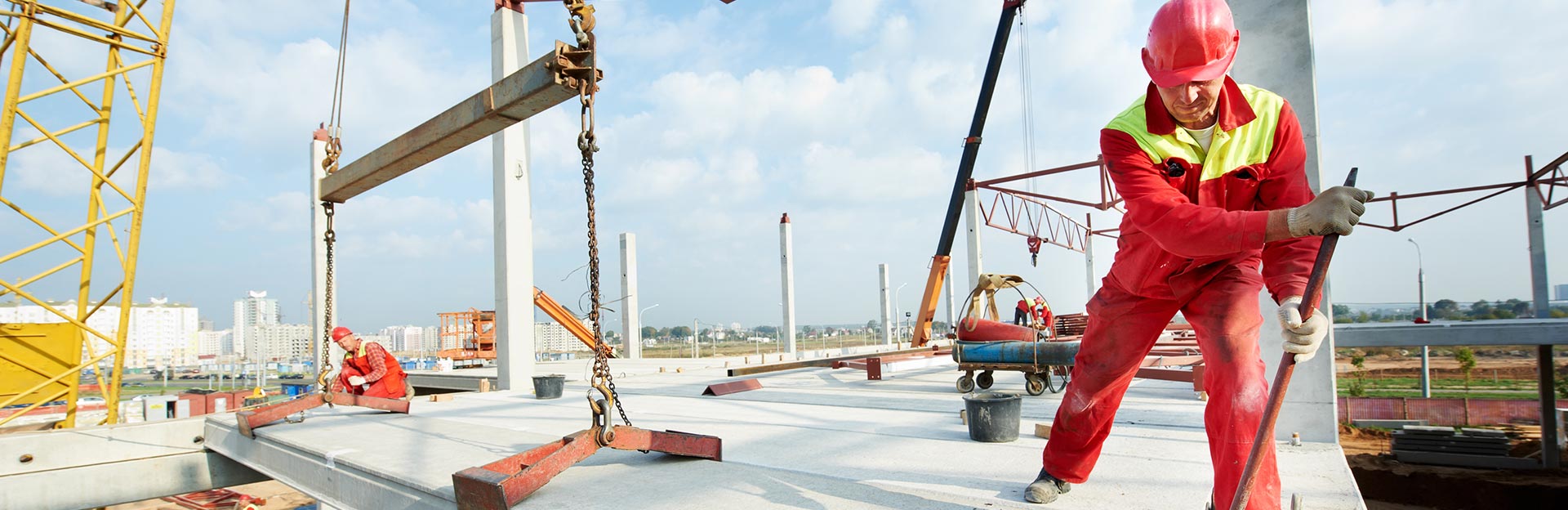

Fall Protection
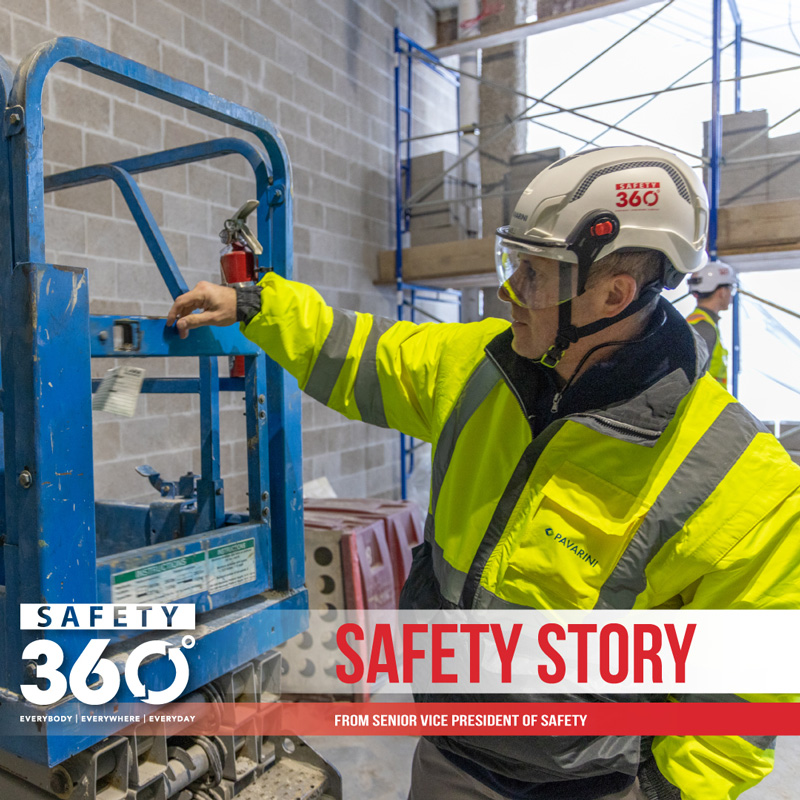
Safety Story from Senior Vice President of Safety, Keith Haselman
Over my career, I have investigated nine falls from Baker staging that was less than 6 feet high—the height that triggers railings or fall protection in our policy. Six of these resulted in significant injuries. In many cases, the worker was leaning too far or handling material that caused him or her to lose their balance.
In discussing the incident with these workers, I asked how they might have prevented their fall. To a person, they said that railings would have prevented it, but that railings would have interfered with their ability to perform their work. I asked if installing railings on three sides or, at a minimum, on the back side might have prevented the fall. Nearly all of them answered yes. When I asked why, they typically responded that a railing would have given them a handhold to catch themselves when they started to lose their balance, or it would have kept their balance inside the deck edge.
Over the years, we have strongly encouraged adding railings to Baker staging below 6 feet as a best practice. Adding railings to Baker staging at all heights is a common practice in New York City.
Falls can cause life-changing injuries that can also result in long-lasting mental health issues. We continue to look into preventing falls and serious injuries through innovations such as podium ladders, smart ladders, light-weight Pico lifts, motorized Baker staging for use on raised floors, safe-and-sound tie-off alarms, and many other tools.
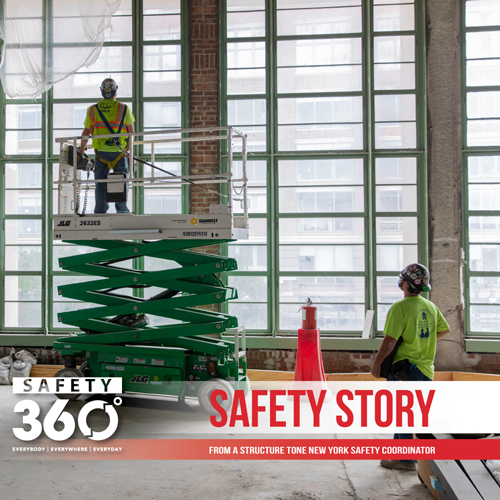
A Safety Story from a Structure Tone New York Safety Coordinator
On a jobsite, several trenches were chopped into the concrete and covered with plywood protection. When three of those trenches on the 8th floor had to be extended to accommodate adjustments to electrical cables, the subcontractor unfortunately did not provide new plywood to cover the now larger holes.
That same day, two workers in lifts were installing ductwork near one of these trenches. I observed one worker moving the lift while in a partially elevated position, unaware of his surroundings below. As a result, the lift’s wheel came within a foot from going into the trench and possibly tipping the lift over. Fortunately, I stopped him right before that happened. I asked him for his credentials and explained that he must always be aware of his surroundings and should fully retract the lift before repositioning it.
As a temporary warning, I placed a cone alongside the open portion of the trench, while the project manager and I immediately contacted the electrical sub to cover the trench as quickly as possible. This instance is why toolbox talks are essential to ensure a safe working environment. Holes on construction sites should always be well-planned, communicated, and covered immediately upon completion of work.
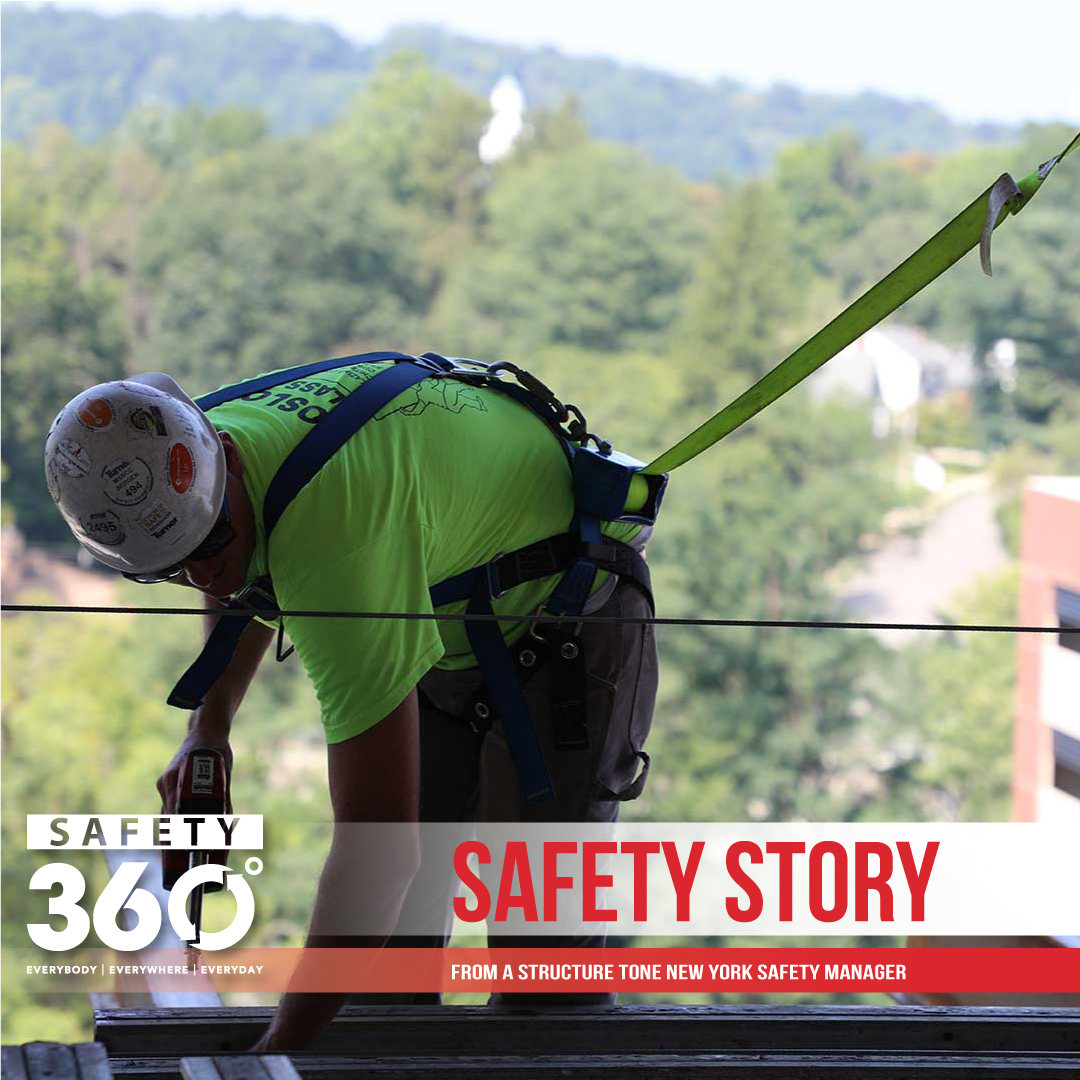
A Safety Story from a Structure Tone New York Safety Manager
Every once in a while, during my walkthroughs at a project, I’d catch the core building installation subcontractor employees working on a suspended scaffold. Because the windowpanes were already installed, I would wave, give a thumbs up or down, and move on. Occasionally, I’d stop and call the foreman to confirm the workers were tied off and had their tools tethered, and nine times out of ten, they were good. However, as humans, we become complacent about our safety from repeated exposure to threatening situations that do not occur.
It was a typical Monday when I walked into work and proceeded to the field. At approximately 10:45am, the Department of Buildings (DOB) issued a high wind weather warning for that evening into the following day. I quickly forwarded the warning to the sites and proceeded to the roof, setbacks, and first-floor park enclosure to confirm we had no loose debris. Once on the ground, I looked up and noticed the suspended scaffold was going up and stopped approximately halfway up the building. I know I did my due diligence and sent out the weather alert, but maybe they didn’t see it? Either way, I felt it was my responsibility to ensure the core installation team knew.
Click to read more
I called the foreman a few times, and he didn’t answer. I then took the hoist to the 26th floor and walked down until I located the suspended scaffold on the 22nd floor. As I got closer to the window, I noticed the foreman wasn’t there. I tried to communicate through the window, but it wasn’t working. I then raised my hand to my head to motion “call,” and he signaled yes with his head. He put his cell phone to the window, and I dialed the employee’s cell number. I asked how he was doing. I also inquired where the foreman was located. He stated that he was out because his wife was going in for emergency surgery. I briefly mentioned the high wind advisory and asked the employees to yank on their fall protection to confirm all were tied in.
One of their longest-tenured employees, whom I had worked with on numerous projects in the past, realized he needed to be tied in and immediately latched his fall protection into the correct tie-off point.
He said, “Come on, give me a break! We just got back from a coffee break. It’s no biggie. Look, I’m tied in now!” I replied, “No issues, just please try and use the buddy system and make sure each of you looks out for each other. I need you guys to go home the same way you got here.” I then proceeded to the ground and went back to the office for a meeting.
At approximately 1:20pm, I get a phone call from the field team. Because I was in a meeting and didn’t want to seem rude, I sent it to voicemail. Immediately after I sent it to voicemail, they called again, and I again sent it to voicemail. I figured they would call me back one more time if it were urgent. Sure enough, they immediately called me back and took the call outside the conference room. I walked outside and picked up, and she frantically stated, “We called 911! A huge gust of wind pulled core install’s scaffold away from the building and slammed it back into the building. The men were on their way down on the north elevation, and another gust of wind came and swung the scaffold around the building onto the east elevation, and now they’re stuck. The fire department is here breaking the windows to help get the employees into the building because the scaffold is stuck!”
I went to my desk, grabbed my hard hat and vest, and ran to the site. There were ten fire trucks, three ambulatory trucks, and five police cars. At that moment, they weren’t letting anyone near the building. They had cordoned off the area due to the broken glass and the scaffold, which was partially in the building. I waited patiently, hoping and praying that my friends were ok. After about an hour, one by one, the core installation employees were wheeled out into their own ambulance. I was overjoyed! As I started to walk away, I heard the employee shout: “Hey, safety lady, hey safety lady, you saved my life!” I gave him a thumbs-up as they wheeled him into the ambulance. You could hear him explaining to the paramedics how he had been reminded to tie in just a few hours ago.
The moral of the story is complacency is a silent killer. Always focus physically and mentally, no matter how many times you may have done the same job. Remember, the time that you are at the greatest risk is when you least expect something bad is about to happen.
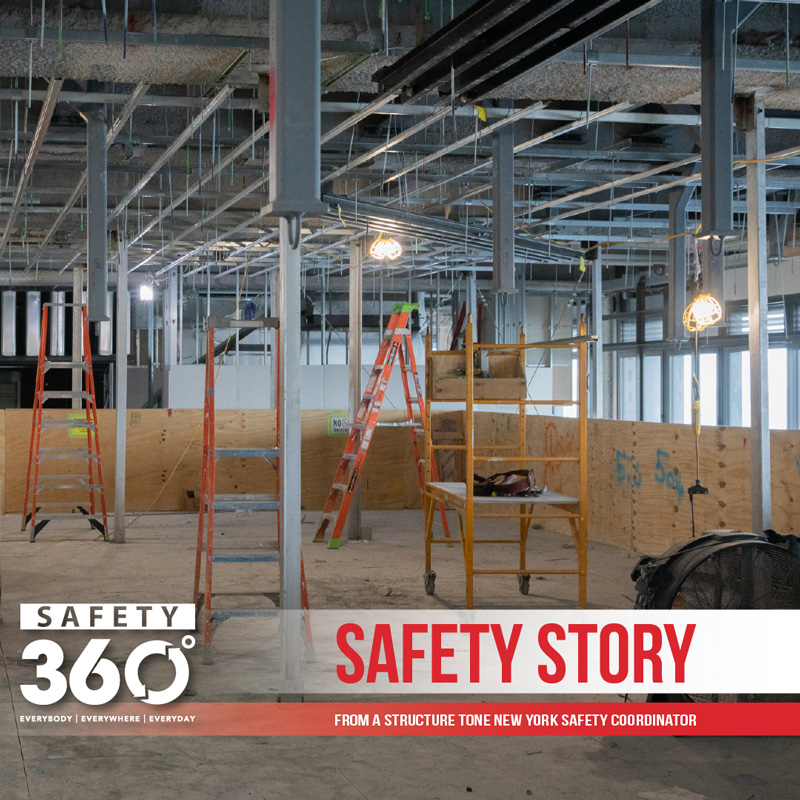
A Safety Story from a Structure Tone New York Safety Coordinator
While walking a floor on my project to conduct my regular safety audits, I observed a worker performing work from a Baker scaffold. The rule when working on a Baker scaffold is that the wheels must be locked, or a person must be assisting the movement of the Baker and locking the wheels after relocating. The worker was not getting off the Baker scaffold and locking the wheels as he moved. Instead, he was manually moving the Baker from the top while leaving the wheels unlocked. This is often referred to as scaffold “surfing.” I approached and held a coaching moment with him, pointing out the dangers of this technique and discussing some of the hazards and injuries related to a Baker tipping over. We also discussed that when someone surfs on a Baker scaffold, they may not detect small elevation changes, debris, hidden holes, etc. in the working surface. If you need to cover a large area and get up and down to move the Baker, you might choose a scissor lift instead or ask for help to be more efficient and ensure your safety.
During our five-minute conversation, he appreciated my advice and my concern for his safety and soon changed his behavior. The next time I saw him, he was dismounting and relocating the scaffold. All construction sites aren’t the same, and even small shortcuts can have long-lasting effects.
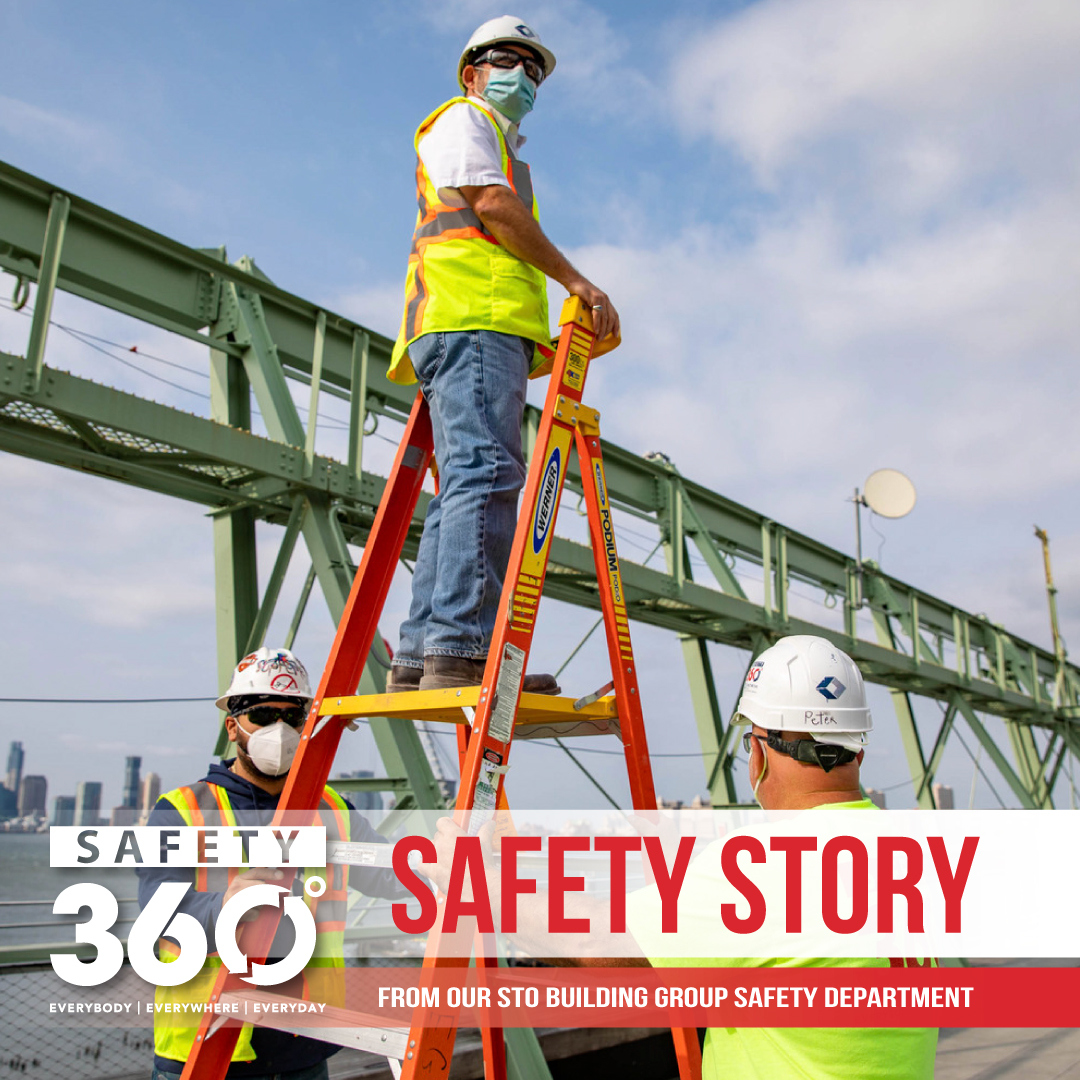
A Safety Story from our STO Building Group Safety Department
Smart Technology and the Future of Ladder Safety
Safety is a core value at STO Building Group, embodied in our Safety 360⁰ program. As part of our innovative culture, we are always searching for new ways of working that reduce or eliminate our risk for injuries to anyone on our project sites. One way we do that is by partnering with external vendors to collaborate on new ways of working. Innovation requires partnerships to deliver new solutions to the market. We are doing just that when it comes to ladders. Since March is National Ladder Safety Month, there’s no better time than now to highlight advancements in ladder safety technology.
Click to read more
Common Tool, Common Hazard
Ladders are an essential piece of daily equipment for construction trade professionals. That frequency of use means ladder-related injuries and accidents are often far too common—in fact, more than 700 ladder injuries occur every day in the United States and falls from ladders are a leading cause of death on construction sites. The estimated annual cost of ladder injuries in the US is $24 billion, including work loss, medical, legal, liability, and pain and suffering-related expenses. Organizations involved in a ladder accident might also be held financially liable for worker injuries even if the cause is not directly linked to the organization (for example, through NYS Labor Law 240/241). These costs might be enough to threaten other workers’ employment and even the viability of the employer organization.One of the most obvious ways a smart ladder could potentially reduce accidents is by notifying the user of a potentially dangerous event. A common example people experience every day is driving an automobile with active blind-spot monitoring. When another vehicle comes too close to the driver, blind-spot monitoring systems notify the driver with an audible noise or flashing light. Just like a blind-spot alert, a smart ladder alert can notify a user that their ladder activity is exceeding the safe tolerances and that they should correct the behavior. Exceeding the ladder’s weight limit, leaning too far to one side, standing on the top steps of the ladder, and climbing on the wrong side of the ladder are a few common examples of unsafe usage. The notifications provide the user with direct feedback and information helpful to avoid preventable accidents.
Climbing Into the Future
An equipment hazard is likely to go unrecognized if the user is unaware the equipment is being used incorrectly. In other words, injuries are much more likely when users aren’t aware they are doing anything wrong. Additionally, safety professionals and supervisors cannot be everywhere at all times and see everything. An automated system that collects data, identifies potentially high-risk use, and notifies workers and responsible supervisors reduces the probability of having an accident due to unidentified hazards. Awareness is a tremendous advantage as it gives the user and others an ability to assess if there is a problem and how any issues might be addressed in advance of negative consequences such as an incident or accident.Connected smart ladders are an excellent example of technology that is within our reach and has the potential to reduce accidents and fatalities, and generally improve the wellbeing of workers and their families. Check out this video about the ladder safety technology we are piloting now: (https://youtu.be/A11tmzUIms0Go to https://nam04.safelinks.protection.outlook.com/?url=https%3A%2F%2Fyoutu.be%2FA11tmzUIms0&data=04%7C01%7CCCascio%40totalsafety.org%7C929ed4181585413b3cd808d9f7bda7cf%7C65f748c079cb46c9b1ebdd186c413ee8%7C1%7C0%7C637813216211723054%7CUnknown%7CTWFpbGZsb3d8eyJWIjoiMC4wLjAwMDAiLCJQIjoiV2luMzIiLCJBTiI6Ik1haWwiLCJXVCI6Mn0%3D%7C3000&sdata=HnYy%2FCi5n%2FHB3n1LixpqyVzKsebsfsfqlJPs42KbG0s%3D&reserved=0).
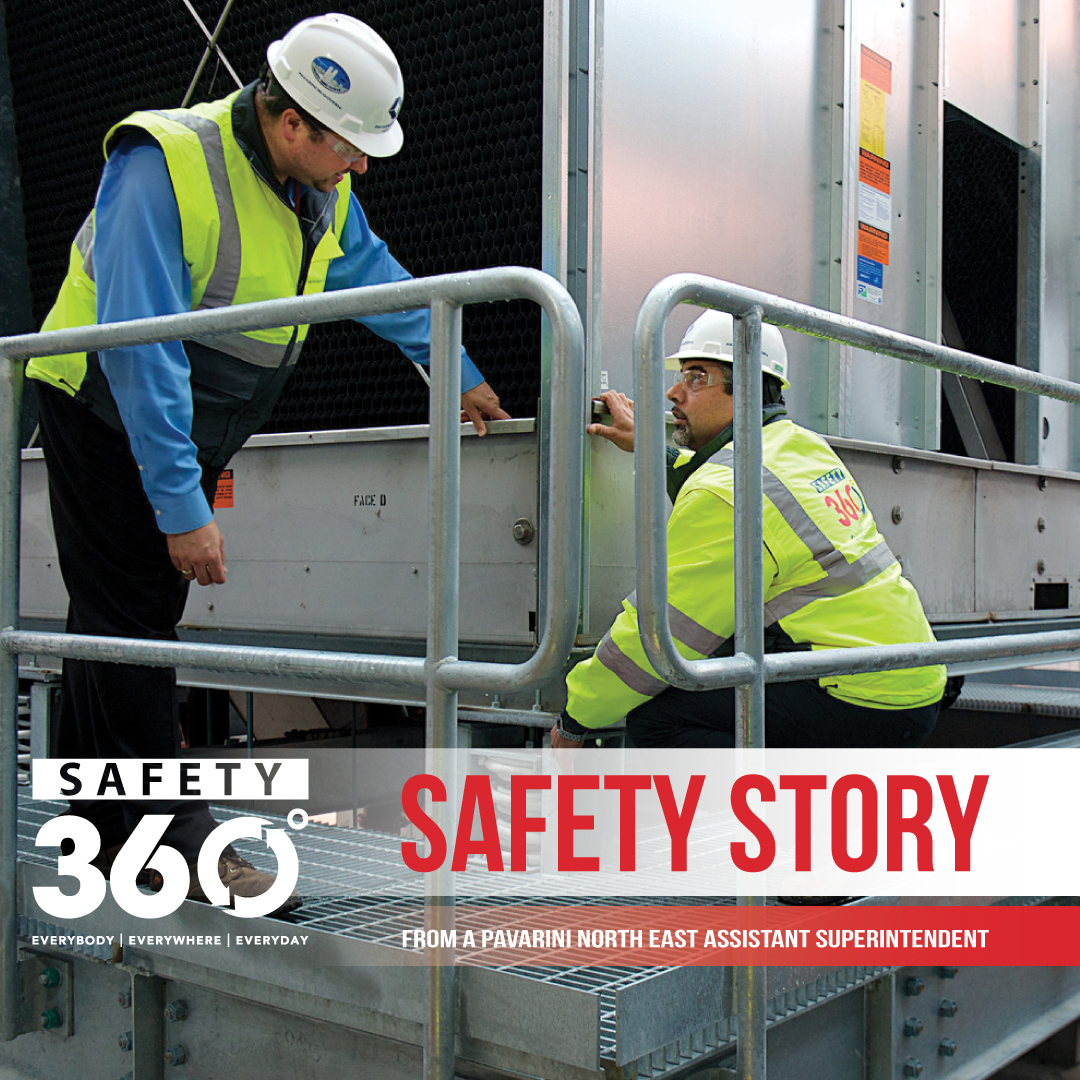
A Safety Story from a Pavarini North East Assistant Superintendent
Week one, we installed floor protection throughout the work area to protect the existing finishes. Meanwhile, our roofing contractor installed fall protection for the roof. The Saturday before the start of work, we held a safety coordination meeting with our mechanical contractor and crane company. We evaluated the scope of work, lift plan, and safety precautions to ensure that the required safety equipment and safety procedures were implemented when operating around the crane and erecting the cooling towers. We double-checked the measurements of the roof opening and the old and new units to ensure that we wouldn’t have any difficulty moving them in and out. After successfully removing the old units and installing the new units, we covered the roof opening in plastic to prevent water damage in the event of rain while double-checking the weather forecast to guarantee that rain was improbable. That Saturday forecast called for a humid day, so we made sure there was water and cool areas to take breaks and that the foremen were keeping an eye on their workers to prevent heat-related accidents. The outcome was a safe and productive day as we achieved all objectives.
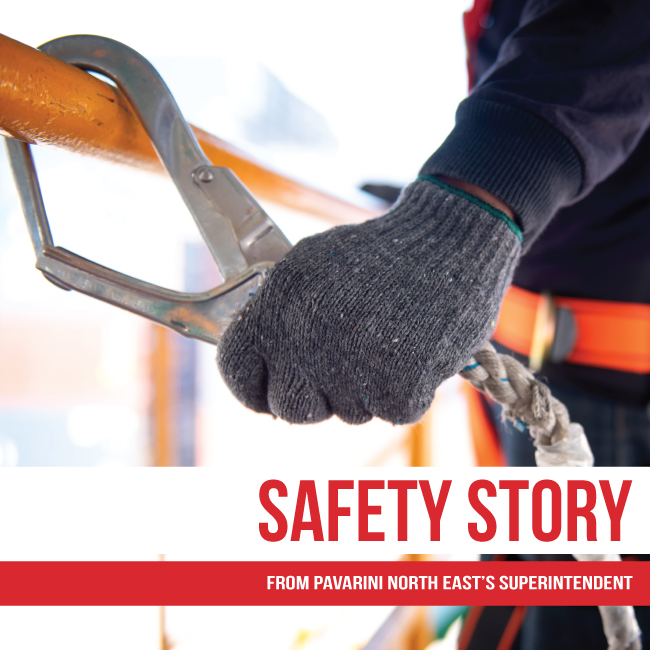
A Safety Story from Pavarini North East’s Superintendent, Brian Butler
Recently, on a PNE project, we worked on a new two-story bank with the top of the roof at 30ft above ground. On the second day of erecting steel, I noticed the ironworker connecting the roof steel was straddling the beam with both feet on the bottom flange and walking to the next beam. As he was bolting the connections, he was wearing a harness that wasn’t tied off. I stopped the project to review safety with the subcontractor. The steel subcontractor did have a 60′ boom lift on site, which the other ironworker used to connect the beams. During our discussion, the foreman noted that OSHA 29CFR 1926.760- Subpart R allows connections up to 30′ in a controlled decking zone. I reminded him that PCC Zero tolerance is anyone above 6′ must tie off. He asked me to confirm with my safety department, and he agreed that his men would use a “beamer” and tie off while I followed up.
I contacted my safety officer, who explained that connectors must have site-specific training for each project, not just connector training. Thankfully, the ironworkers were tied off for the remainder of the project.
A Safety Story from Structure Tone Philadelphia laborer:
When a Structure Tone Philadelphia laborer noticed window washers had tied off to the wrong turrets, he immediately took action. Watch the video to hear him tell his story.
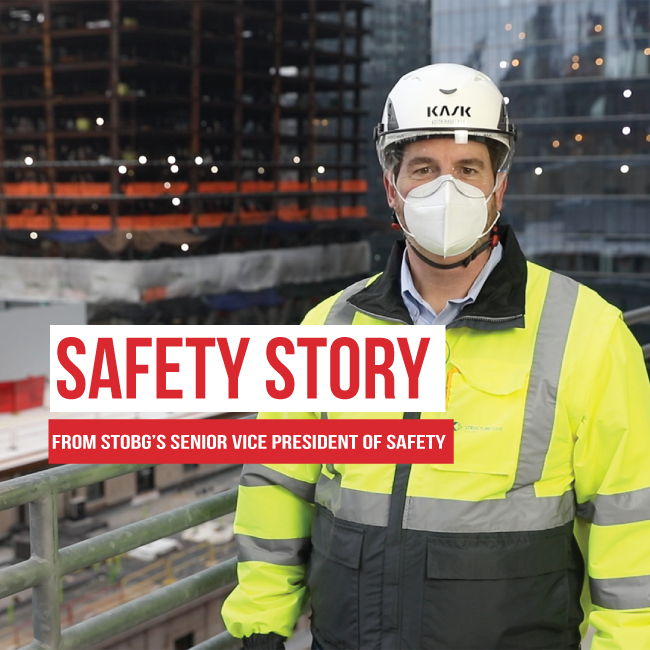
A Safety Story from STO Building Group’s Senior Vice President of Safety, Keith Haselman
My friend Jim, a fellow pilot in Pensacola, Florida, was newly engaged and had just bought a new house. He found squirrels had eaten a hole through the cedar siding and were in the attic. His first trip up, he missed the joist and his foot went through the ceiling. Embarrassed, he called me over to help with the issue. He stated he chased the squirrels out but needed to borrow my extension ladder to temporarily seal the siding. I stepped the base of the ladder as Jim went up to spray foam to seal the hole before installing a temporary lap board. He was just about to place the board over the hole when a terrified squirrel, still in the attic, suddenly shot out of the foam and landed on his chest before launching away.
Jim, in a sudden panic, swung sideways but kept a hand on the ladder as I fought to maintain it, while the nails and board dropped from above. He quickly swung back, descended, and thanked me for the save. Then, he paused and stated, “That was terrifying.”
Having one extra person added a layer of safety that may have prevented a disabling injury.
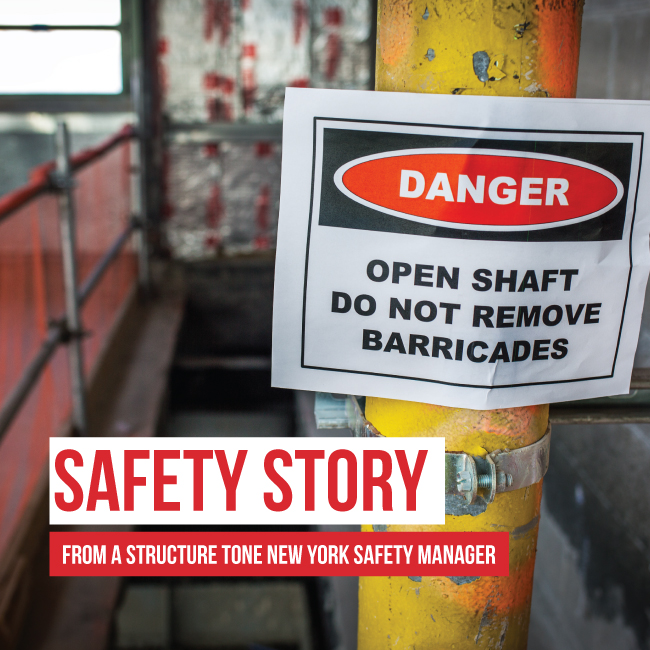
A Safety Story from Structure Tone New York Safety Manager, Bill Coddington
I started my career at Structure Tone in the late 1990s. Through the years, I’ve worked as a laborer, superintendent, a general super, and currently, as a safety manager in NYC. At the time this story occurred, I had only been with Structure Tone for a year or two, and I was a laborer assigned to a small project on Crosby Street. The building we were working in was installing a new modern hydraulic elevator to replace the manually operated, two-person traction elevator.
This day started like every other. Our project was on the top floor, which was the fourth floor of this building. I walked over to the shaft, which had a barricade of two-by-fours across the openings, and I looked in to see what floor the elevator installers were working on. The elevator rails had been installed, as well as the cars in the two connecting shafts. The workers were installing the sills at each landing, as well as the doors. This particular morning turned out to be very different. As I leaned against the top wood rail across the opening of the shaft, it immediately gave way. The mid-rail, still snug in its cradle, ensured my momentum would send me headfirst into the darkness. It turned out, one of the elevator installers had removed one side of the rail from its cradle, resting it on top of the cradle. They say your life flashes before your eyes when you have a near death experience. It didn’t in my case because in an instant, I fell onto the top of the new elevator car, which had been parked just below the floor I was working on, thankfully.
I fell about six feet onto the new car. The top of an elevator has steel running across at different heights, as well as many other pieces of metal and equipment, so I was hurt but alive. The crew working on the car knew immediately what happened and came to my aid. I remember getting helped off the top of the car onto the floor, and just sitting and crying—partly because of the pain I was in, but mostly because my thoughts went to my wife, who was expecting our first son. The young elevator installer who removed the rail that morning was as upset as I was. He still calls me a couple of times a year just to say hello.
I knew that leaning on a guardrail was wrong but had done it anyway, and almost paid with my life. If that car had not been parked where it was, I would not be able to share this. We all can benefit from other people’s experiences. I am certain this is why I have always gravitated towards safety. Please be safe out there.
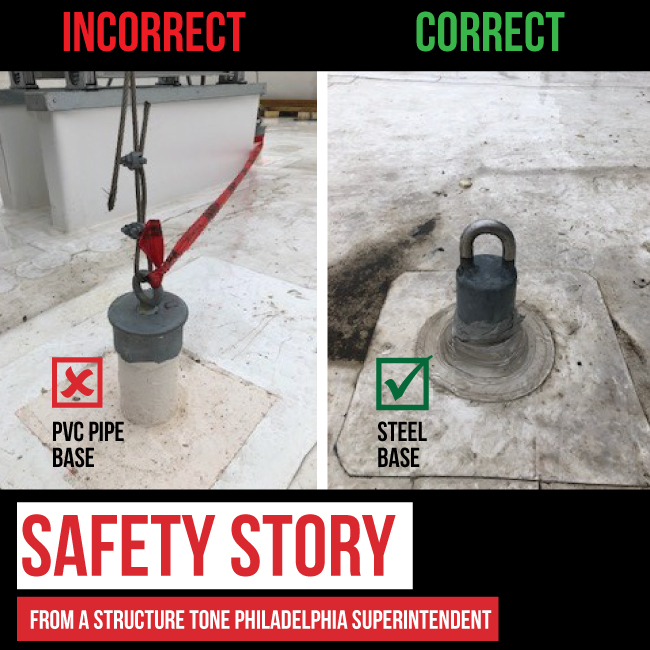
A Safety Story from a Structure Tone Philadelphia Superintendent
One Saturday last February, a Structure Tone laborer in Philadelphia headed to his site on the roof of a prominent office building in the city’s central business district to button down any loose material due to incoming windy weather. When he arrived, the building’s window washers were hanging from the roof to clean the windows below. During the inspection, he noticed one of the window washers’ lifelines was connected to a roof anchor base made of PVC, instead of the approved steel anchor that’s imbedded into the roof’s concrete. The laborer immediately went to the roof’s edge, which had a 48-inch parapet, and notified the window washer of the tie-off mistake. The window washer was already six stories down the 14-story structure and quickly descended to safety. The laborer may have saved this window washer’s life, all because he saw something that didn’t look right and took action. As a result of the incident, the window washers created a new standard to confirm the approved roof anchors with each building they work with.
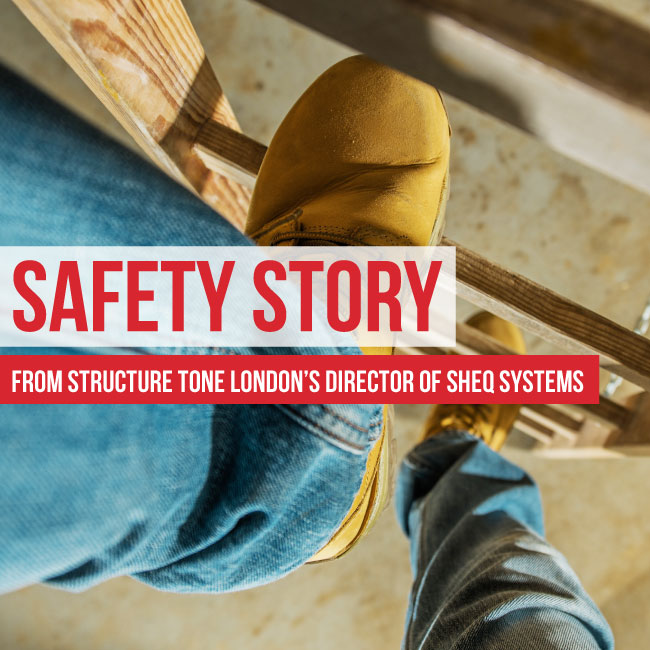
Safety Story from Structure Tone London’s Director of SHEQ Systems
A friend of mine has worked in highway engineering for three decades and is a firm advocate of his company’s workplace safety culture. However, a few months ago, my friend sustained serious injuries, including a punctured and collapsed lung and nine broken ribs, after falling from a ladder.
He had been trimming back some bushes at his Cheshunt home when the ladder wobbled, and he decided to jump clear from it. In hindsight, he knows that wasn’t the right decision—it should have been a two-person job so someone could hold the ladder.
After two stays and 23 nights in the hospital, my friend recovered with the support of his family, friends, and colleagues. Now back at work, he preaches safety 24/7, not just in the workplace.
“People don’t think about the consequences an accident can have on you and your family,” he said. “This accident could have been avoided, and that will live with me forever.”
Safety at work is always a top priority, but this is a reminder to apply the same safety principles while taking on odd jobs at home as well.
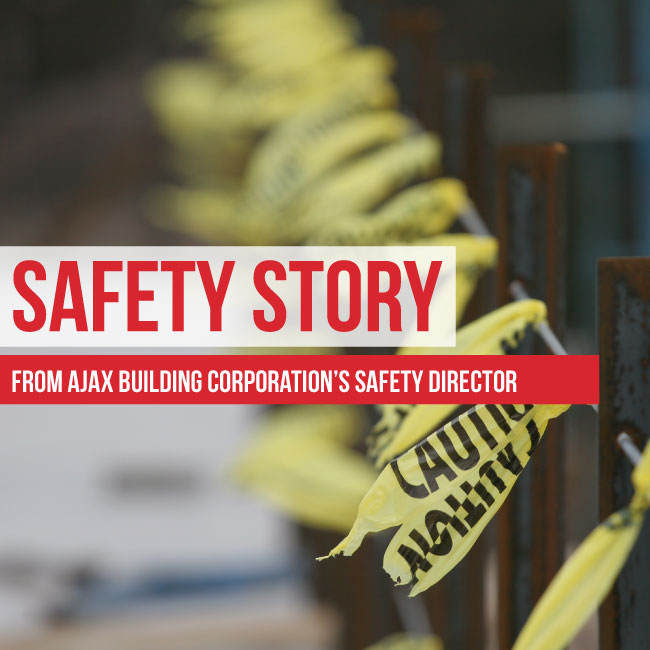
Safety Story from Ajax Building Corporation’s Safety Director
A few years ago, Ajax was working with a particular steel erector for the first time on a project in Charlotte County. Whether it was getting everyone to wear their PPEGo to https://stobuildinggroup.com/safety-stories-ppe/ or enforcing proper fall protection practices, making sure the foreman and crew were working safely was a daily struggle. Throughout the project, we held numerous meetings to discuss safety compliance, and when that failed, we were forced to start sending crew members home for violating site safety requirements. We even assigned a full-time safety coordinator to the project, specifically to monitor this crew.
About two years later, we were starting another project in Pinellas County. Market realities at the time dictated that we expand our base of steel erection subcontractors, so we hesitantly hired the same steel erector. We conducted a pre-construction safety meeting with them prior to starting and—as luck would have it—the same foreman and crew who had been on the last project were also assigned to this project.
During the meeting, I went through all the usual safety topics and the crew was fully engaged. Afterwards, the foreman pulled me aside and told me a serious incident occurred on the project immediately following their first job with Ajax. The event motivated them to hire a full-time safety director and develop safety training programs for all workers. “That accident opened our eyes, but it started with you guys,” the foremen said. “Ajax and your insistence on us working safely made us a better company.”
They ended up being one of the top subcontractors on that project and are now one of our “go-to” steel erection subcontractors.